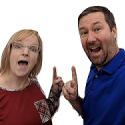
Peter and Bud - Upset Circuit
Started by
TimWilborne,
28 posts in this topic
Create an account or sign in to comment
You need to be a member in order to leave a comment
Started by
TimWilborne,
You need to be a member in order to leave a comment