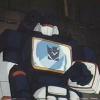
CJ1M High Speed Counter
Started by
soundwave,
15 posts in this topic
Create an account or sign in to comment
You need to be a member in order to leave a comment
Started by
soundwave,
You need to be a member in order to leave a comment