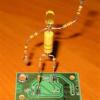
programmable or specific controller?
Started by
justwhy2003,
10 posts in this topic
Create an account or sign in to comment
You need to be a member in order to leave a comment
Started by
justwhy2003,
You need to be a member in order to leave a comment