
Joe E.
MrPLC Member-
Content count
1593 -
Joined
-
Last visited
Posts posted by Joe E.
-
-
If all you want is to store good/bad, use a bit shift array using a BSL or BSR instruction.
High level description:
You'll execute the BSL/BSR once per "interval" of the conveyor's movement. Let's say the end position is at bit 0 of the array and the sensor is at bit 20. The sensor will set/reset bit 20 of the array while the reject/whatever sequence looks at bit 0. A BSR is fired to shift the data automatically. -
2 hours ago, pturmel said:... (The dual ports on AB devices should only be used for real rings.)...
I've seen many applications that used the dual ports in a daisy-chain configuration. Is the main drawback that all downstream devices go away if one in the middle is powered off? Or is there another reason too?
-
Are the products all the same size? If so, I would first create an array big enough to have one position for each place a product could be on the conveyor. Array could be bits or integers, depending on how much info you want to track. Use the encoder to advance the array. Write to the right spot in the array at the sensor and read from it at the "store" position.
That's my first pass thought.
-
I replied to your PM.
-
I've been in the habit of running all of my automation software in virtual machines since about 2011 or so. If that's the only software you need, you could try it on Win11 and it will most likely be just fine even though it's not officially supported. If you ever need to run more software packages in the future, though, I would seriously recommend virtual machines.
2 people like this -
There's a tech note (access level: TechConnect):
https://rockwellautomation.custhelp.com/app/answers/answer_view/a_id/1136965/loc/en_US#__highlight
Several things to try are listed there. -
Interesting...I'm not sure if I have that problem or not, but my test bench 1769-L33ER (v34.11) is 2.5 hours fast right now. It's been a while since I checked the CPU time, so it may have been drifting for a very long time.
-
Well, there I go not spending enough time reading the details...
-
4 hours ago, pturmel said:Wrong Anybus. This one, I think:
Isn't that for a Profibus slave? OP wants to connect a Modbus RTU Slave to a Profibus Master
-
No personal endorsement, but I've seen other products from Anybus that seemed solid:
https://www.anybus.com/products/gateway-index/anybus-xgateway/detail/anybus-x-gateway-profibus-master-modbus-rtu-slave
Do you think that one might work? I checked ProSoft first but they only have Profibus to Modbus TCP, not RTU. -
What version of TIA Portal are you using? Do you have WinCC Basic? I don't have that software any more, but I do remember it being version sensitive. But that may have changed with newer versions.
1 person likes this -
Here's just lad 2. It printed the whole thing when just doing an individual ladder file.
-
That's crazy. The preview shows all rungs, and I could have sworn I double checked the pdf but it's not there.
-
I think you're going to have trouble with that distance. Just as a reference, I pulled up the guidelines for Rockwell drives (because they're handy) and the max distance they support with filtering varies by size and series of drive but maxes out at 365m or so.
https://literature.rockwellautomation.com/idc/groups/literature/documents/in/drives-in001_-en-p.pdf
Your distance is almost 6 times longer than that. Definitely reach out to your drive manufacturer for guidance. You may end up having to build an enclosure near the pond for the drive.
1 person likes this -
Try this. "Microsoft Print to PDF" is pretty awful, it seems. Some pages ended up missing and the file size always seems huge.
-
Hmmmm, that is weird. I told it to print the whole thing but it looks like it didn't work right. LAD 2 has 140 rungs. Let me try again with a different print driver.
-
-
I generally find myself using IPAssign from Phoenix Contact more than AB's Boot/P. It tends to work well at assigning the address. I then use RSLinx to disable DHCP.
1 person likes this -
Thanks for that info. It seems a little crazy that the BootP tool has to be upgraded. Shouldn't it just be supplying IP addresses? Maybe the command to disable DHCP is special...
-
We ordered 9324-RLDMLPE, the Multi-language pack that licenses use of ST, FBD, and SFC. It's an add-on to the standard edition license that lets us use the other programming languages. There may be something you can order to just get ST, but I'd probably just get the multi-pack. You'd have to reach out to your local distributor to find out. You'll need to talk to them for pricing anyway, and AB's licensing system is messy enough you'll want expert assistance getting the right thing.
-
A couple of times, I had to wait a bit and try again when attaching multiple files.
-
The manual itself doesn't provide much info but it links to an Excel spreadsheet with a little more info:
https://literature.rockwellautomation.com/idc/groups/literature/documents/rd/2198-rd005_-en-p.xlsxFor "NODE FLT 02 – PROC WATCHDOG nn", the spreadsheet says:
QuoteFault:
Processor Watchdog Fault
The processor on the power board or control board failed to update in a certain amount of time.
The Possible Solutions are the same for all nn sub-codes.
Action:
• Cycle control power
• Return drive for repair if fault continuesDid you find this tech note (access level: TechConnect):
https://rockwellautomation.custhelp.com/app/answers/answer_view/a_id/635513/loc/en_US#__highlight
It adds another possible fix:
QuoteUpgrade firmware, or reflash drive with current firmware
1 person likes this -
Some faults will cause the PLC to erase the program in memory. Without going online with the software while the fault is active, it's hard to be more specific.
The 1400 has an LCD screen where you can navigate to "Monitoring" and select file #2, which is processor status. You can then look at individual words. Word s:6 is your major error code. I've never used the LCD to diagnose an issue since it's easier with the software so I don't know if the LCD still works when the processor is faulted, but that's where I would go if I didn't have a license.
1 person likes this -
I found a comparison tech note (access level: everyone) that compares them:
https://rockwellautomation.custhelp.com/app/answers/answer_view/a_id/1032455/loc/en_US#__highlight
It doesn't show a difference that should affect trending, but there could be other things different.
There's another more detailed comparison document here:
https://literature.rockwellautomation.com/idc/groups/literature/documents/sp/2711p-sp011_-en-p.pdf
That one also doesn't mention trending or datalogs.
Tracking,
in Allen Bradley / Rockwell Automation
Posted
So, some more details. The BSL and BSR instructions operate on a rising edge of the rung enable. You would enable the instruction once every time the encoder turns enough for a part to have passed by.
The last one I did is in a CompactLogix. I had to create a tag called "Track_Array" of type DINT[1]. The Array tag of the BSL instruction was Track_Array[0]. Its Control tag is a new otherwise unused tag and the source bit (for me) is an Always_Off bit. Length is the number of parts that can be on the conveyor plus a few. If the conveyor is more than 32 parts long, you'll want to have your Track_Array tag bigger. For example, DINT[2] will get you 64 positions. The one I did was anchored at the load station being station 0 so I used a BSL. If instead you want the end to be bit 0, you'd use a BSR instead. Doesn't really affect things other than how you think of it.
Here's the rung with the BSL. CAM_00 is on once per machine cycle. In your case, you'd flash it once every time a part spot has passed by on the conveyor:
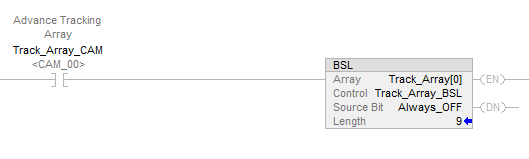
Here, we set bit 1, which is where the servo loads the blanks:
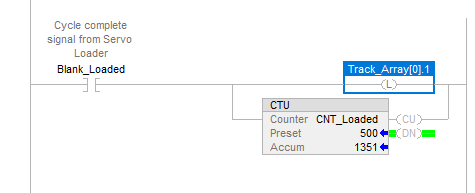
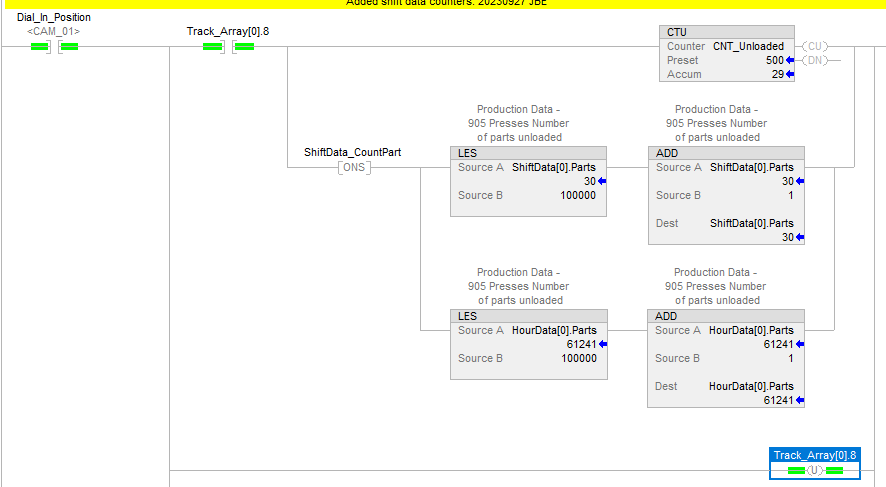
Here, we clear bit 8, which is where the finished parts fall out of the machine.
Like I said before, I'm not 100% sure this is really the best way to proceed for you. It may make more sense to use a FIFO array. Use an FFL instruction every time a part passes by the sensor and an FFU every time a part arrives at the end position.
Downside to using a BSL/BSR is if the parts can slip on the conveyor. If that's not an issue, the FIFO won't work if parts can be removed from the conveyor between the sensor and end. That's why it's good to have multiple tools in your belt.